1 Background
Formula Student is one of the most demanding engineering competitions in the world, pushing student teams to design, build, and race high-performance prototype vehicles under strict technical regulations and tight timelines.
In such a competitive environment, every factor helping to maximize the vehicle’s performance is very valuable. One of the key enablers of high performance is the ability to accurately and reliably estimate the state of the vehicle at all times. Knowing quantities such as velocity, acceleration, yaw rate, wheel slip, and even tire forces in real time can make the difference between a car that simply moves and one that performs at the limit of its capabilities.
Additionally, with the disruption of autonomous racing in the past years of Formula Student, accurate state estimation becomes critical not only for the advanced control and pushing of the car’s dynamics but also for the stability and safety of the autonomous navigation. In our particular case, to face these challenges, we have developed a state estimation module that performs sensor fusion by means of an Extended Kalman Filter (EKF). In there, data from our IMU, wheel encoders, torques, and steering is employed to estimate accurate speeds. Gently, Sensoric Solutions has let us test their OMS Race ground speed sensor, which, for the first time, has allowed us to compare the outputs of our state estimation node to actual ground truth data.
2 Set Up Experience
The compact design of both the sensor unit and the ECU significantly eased the process of integrating the system into our vehicle. Their relatively small size allowed us to choose mounting locations that were both mechanically robust and electrically convenient for us. Regarding the sensor, we decided to install it close to the rear left wheel, mounted just behind the aero side structure, as illustrated in Figure 1. For this, we crafted a custom in-house aluminum mounting plate, designed specifically to interface with the car’s monocoque structure. The ECU, on the other hand, was mounted within the front compartment of the car, where it was securely fixed and directly connected to our low-voltage power supply and the car’s CAN bus.
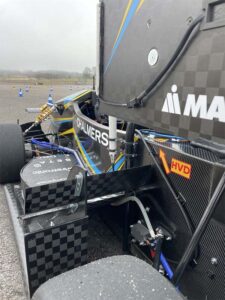
Sensor’s mounting on the vehicle

Close up of the sensor mounting
We really appreciate the configuration software provided for the sensor since it was par ticularly user-friendly and intuitive. During the initial setup phase, we were able to easily define the sensor’s position relative to the desired point of interest (POI), ensuring that all measured data would be correctly translated to our car’s COG. Additionally, the correction of the mounting angle offset was easily carried out during our first testing session and input into the sensor’s software without difficulties.
It was also highly appreciated that the CAN DBC file for the sensor was provided. This greatly simplified the process of integrating the sensor data into our existing CAN logging system, enabling fast and seamless communication with our data acquisition infrastructure.
That said, one area where we believe there is room for improvement is a bit of clarification in some areas in the documentation. While the manual covers the basics very well, we found that several of the sensor signals listed lacked detailed explanations regarding their meaning or intended use. Additionally, a more comprehensive description, or just a schematic, of the reference coordinate system that is referred in the sensor signal descriptions would have been very clarifying.
3 Testing and Measurement Data
In total, we conducted 46.3 km of autonomous driving tests and 32.8 km of manual driving tests. These sessions were designed to explore a broad range of operating conditions and vehicle behaviors.
Our primary objective was to assess the accuracy of our state estimation node, particularly focusing on the speed estimations. In addition to that, we aimed to evaluate the potential performance benefits of incorporating accurate slip angle measurements into our tire modeling and control strategies.
In order to conduct a thorough validation, we tested the vehicle under various dynamic conditions. Those included, a range of different vehicle dynamics set-ups (e.g., suspension, anti-roll bar stiffness…), both dynamic driving and a wide range of different steady-state maneuvers. As well as different torque vectoring approaches.
As shown in Figure 2, our most significant finding was the contrast in estimation accuracy between the longitudinal and lateral velocity components. While the EKF provided reliable estimates for the longitudinal velocity (vx), the lateral velocity (vy) showed noticeable discrepancies. These inaccuracies in the vy estimation would have a large negative impact on the quality of derived quantities such as slip angles, which are critical for example if you aim to have a high performance adaptive velocity planner for your autonomous longitudinal control.
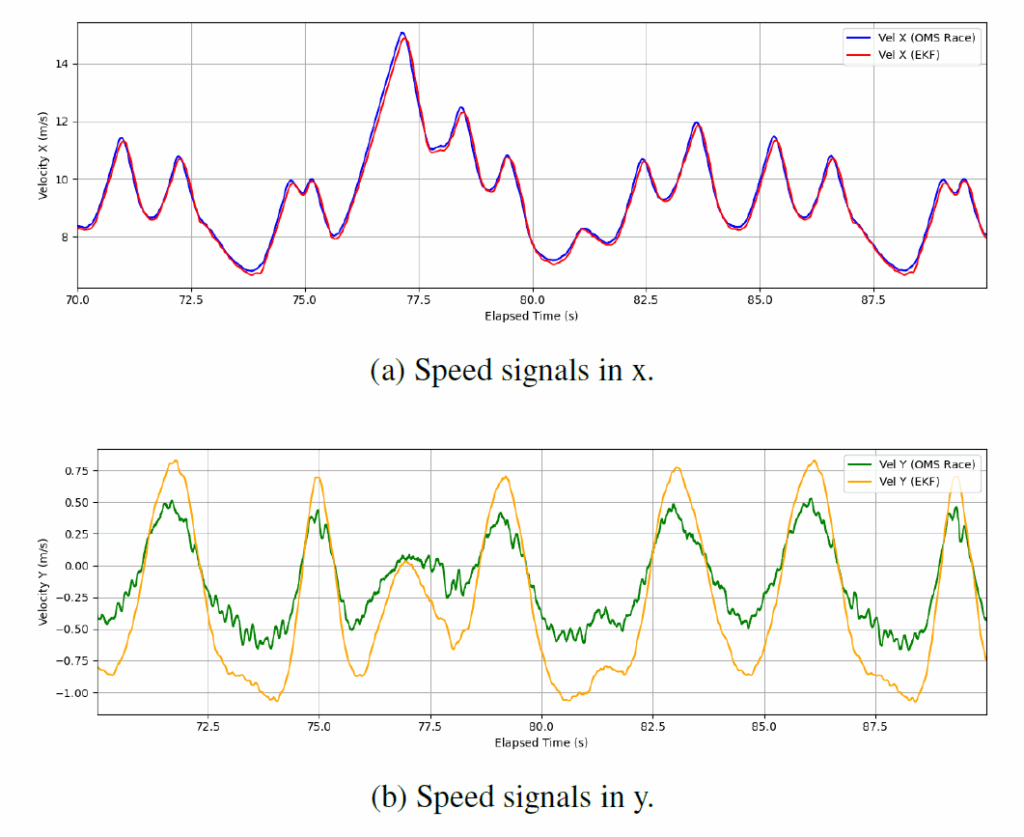
Speed measurements from OMS Race and the estimations from our EKF
4 Summary
The OMS Race Sensor proved to be a compact, well-designed, and highly valuable device for our application. Its ease of integration and intuitive configuration software made it straight forward to install and calibrate within the packaging constraints of a Formula Student car.
Thanks to the opportunity to test the sensor, we were able to collect high-quality data under a wide range of driving scenarios. This data has been incredibly useful in identifying and later resolving inaccuracies inside our state estimation module. This has not only allowed us to refine and validate our EKF but will also directly contribute to the development of more accurate models and control approaches for our vehicle.
We would like to express our gratitude to Sensoric Solution for providing us with access to their OMS Race sensor. Having the opportunity to work with such a professional piece of hardware was not only technically rewarding but also an instructive and motivating experience. We believe this sensor can be a valuable asset for any team looking to validate and improve their estimation and control systems.